Polyethylene (PE) is one of the most widely used plastics in injection molding applications, from food packaging and containers to automotive parts and household goods. Unlike many other polymers, polyethylene does not absorb significant moisture from the atmosphere. So does polyethylene actually need to be dried prior to injection molding? As a professional plastic injection molding manufacturer, I will help you dive into the details.
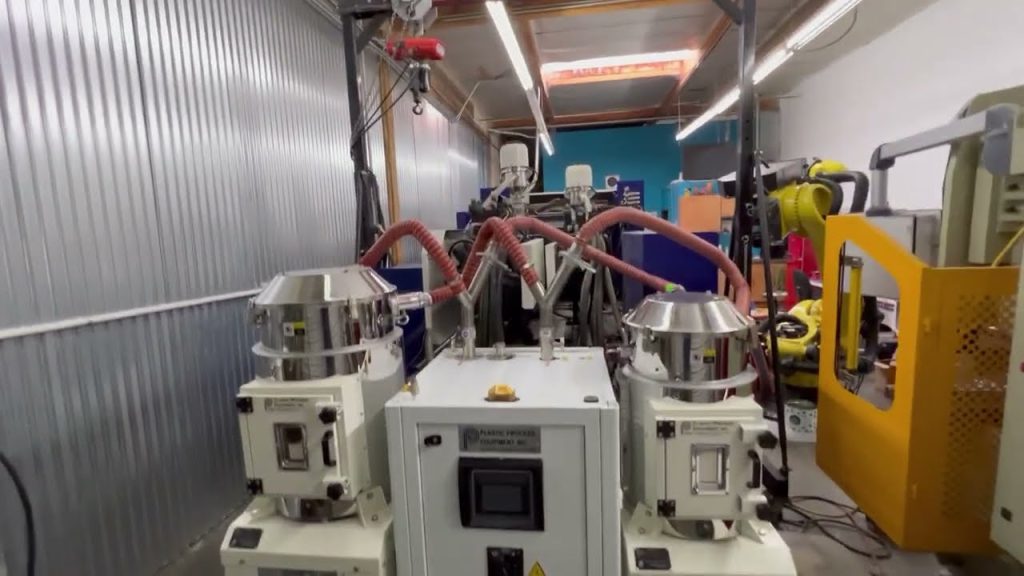
Does Polyethylene Need to Be Dried for Injection Molding?
Polyethylene and other polyolefins like polypropylene are classified as non-hygroscopic materials. This means they do not tend to absorb ambient moisture into their bulk.
So technically, pure polyethylene resins do not need to be dried before injection molding. Drying polyethylene is generally unnecessary as moisture absorption is quite low compared to hygroscopic resins like nylon, PET, and polycarbonate.
However, while the bulk polyethylene pellets contain negligible moisture, condensation can sometimes occur on their surface if exposed to significant temperature or humidity changes during storage and handling. This superficial moisture should be removed to prevent potential processing issues or surface defects.
When Might Drying Polyethylene Be Required?
Here are a few scenarios where drying your polyethylene prior to injection molding could be warranted:
- The resin pellets accumulated surface moisture from temperature/humidity fluctuations during transportation or storage. Surface moisture can interfere with plastication in the barrel.
- You are molding polyethylene compounds or blends containing small amounts of moisture-sensitive polymers like EVAs. Here, even low levels of moisture absorbed by the secondary polymer may need to be removed.
- Your facility is located in a high temperature/humidity environment. Ambient moisture condensing on the cool resin during handling may need to be eliminated, even for polyolefins.
- You intend to use previously recovered and recycled polyethylene, which could absorb some moisture during prior processing.
- Your product requirements demand maximum performance consistency. In highly regulated industries like medical devices, drying polyethylene as a precaution before molding may be warranted.
- There are special circumstances like long residence times in the barrel, very fast cycle times, or other unique processing conditions that could be impacted by trace moisture.
What Happens If Polyethylene Is Molded Wet?
If polyethylene resin containing surface moisture or other volatile residues from recycling is molded without drying, common defects include:
- Surface imperfections like streaking, micro-bubbles, and flow marks
- Visual quality issues caused by volatiles forming gas during plastication
- Potential minor variations in melt viscosity and flow
However, unlike truly hygroscopic resins, molding polyethylene resins with moisture does not typically compromise mechanical properties or part performance. And the potential for hydrolysis reactions degrading the polymer chains is non-existent with non-polar polyolefin chains.
What Are Appropriate Drying Conditions for Polyethylene?
While extensive drying is unnecessary for polyethylene prior to injection molding, removing any superficial moisture on the pellets requires far less energy than hygroscopic resins.
Here are some typical guidelines:
- Temperature: 140°F to 175°F (60°C – 80°C)
- Time: 2 to 4 hours
- Dewpoint: No desiccant drying required, ambient air is sufficient
Maintaining temperatures below 180°F (82°C) prevents potential heat degradation and melting complications during handling. Monitoring the drying process visually and confirming no remaining surface moisture through tactile inspection is reasonable for polyethylene.
Conclusion: Should You Dry Polyethylene or Not?
To recap, most grades of neat polyethylene resin do not need extensive drying before injection molding under normal circumstances. Traces of surface moisture that may condense on the pellets can often be eliminated through gentle warming in ambient air above the boiling point of water.
However, particular applications with tighter quality requirements, performance consistency needs, or where trace moisture could interact with minor secondary polymer components may still benefit from a brief, low temperature polyethylene drying step.
Proactive drying can be considered inexpensive insurance against potential processing defects or performance deviations in mission-critical polyethylene applications. But extensive drying regimens are generally excessive and provide no significant advantage for polyolefin molding.